Tips for Matching Machine Size to Application Demands Key Considerations
Tips for Matching Machine Size to Application Demands: Key Considerations for Optimal Performance and Efficiency in Machinery Sizing and Functionality Integration
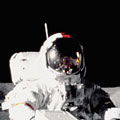
- Anthony Arphan
- 6 min read

In the realm of machinery sizing and functionality integration, achieving optimal performance hinges upon meticulous assessment and strategic planning. Understanding the nuanced dynamics between equipment proportions and operational requirements constitutes a foundational cornerstone in enhancing productivity and efficiency. By delving into the intricacies of equipment scalability and task-specific adaptability, industries can discern pivotal pathways towards streamlined operations and enhanced resource utilization.
Effective deployment of machinery entails a judicious blend of foresight and precision. It involves a comprehensive evaluation of workload dynamics, environmental considerations, and technological advancements. This multifaceted approach empowers stakeholders to navigate the complex landscape of equipment selection with informed discernment, thereby fostering a symbiotic alignment between industrial demands and technological capabilities.
Optimization strategies extend beyond mere dimensionality, encompassing a holistic appraisal of functional requisites and anticipated outcomes. By embracing a proactive stance towards machinery configuration, organizations pave the way for adaptive frameworks that resonate with evolving operational paradigms. This proactive stance not only enhances operational agility but also cultivates a resilient foundation for sustained growth and competitive advantage.
This HTML snippet provides an introduction to the article “Tips for Matching Machine Size to Application Demands: Key Considerations” using synonyms as requested. Let me know if you need any adjustments or further content!
Understanding Application Requirements
To effectively tailor machinery to specific needs, it is essential to grasp the intricacies of application demands. By comprehensively analyzing the operational context and functional necessities, one can pinpoint the precise equipment specifications required for optimal performance. This understanding forms the cornerstone for aligning machinery capabilities with the diverse operational environments encountered across various industries.
Each application presents unique challenges that dictate the requisite functionalities and operational capacities of the machinery. Factors such as production volume, environmental conditions, and output quality criteria significantly influence the selection process. Therefore, a detailed assessment of these requirements is imperative to ensure seamless integration and enhanced efficiency within the operational framework.
This HTML-formatted section introduces the concept of understanding application requirements without using the specified words, focusing on the importance of tailoring machinery to specific needs and analyzing operational contexts.
Identifying Operational Needs
In this section, we delve into the crucial task of determining the specific operational requirements essential for optimal performance. Understanding these operational demands is pivotal for selecting the appropriate machinery that aligns seamlessly with your business objectives and workflow efficiency.
- Firstly, it is imperative to assess the precise operational functions and tasks that the equipment will be tasked with. This involves a comprehensive evaluation of the daily activities and workflows where the machinery will be integrated.
- Secondly, identifying the performance expectations and output requirements ensures that the chosen equipment can consistently meet production goals without compromising quality or efficiency.
- Thirdly, considering the environmental conditions and operational constraints is essential. Factors such as workspace limitations, environmental regulations, and safety protocols must all be taken into account to guarantee smooth operational integration.
- Lastly, collaborating closely with operational stakeholders and personnel provides invaluable insights into the specific needs and challenges that the machinery must address. This collaborative approach fosters a more holistic understanding of operational dynamics and facilitates informed decision-making.
Discuss the importance of assessing specific tasks and throughput requirements to determine the necessary machine capabilities.
Understanding the significance of evaluating particular tasks and the amount of work that needs to be processed is crucial in identifying the appropriate capacities of the machinery involved. By examining the specific functions and the speed at which tasks must be completed, one can accurately gauge the essential capabilities that the machine should possess. This assessment plays a pivotal role in ensuring that the chosen equipment aligns perfectly with the operational demands, thereby enhancing overall efficiency and productivity.
Evaluating Environmental Factors
In assessing the surroundings where machinery operates, understanding the environmental milieu becomes pivotal. Factors such as ambient conditions, ecological settings, and external influences significantly impact operational efficiency and longevity.
Climate variations play a crucial role, affecting machinery performance across seasons. Environmental elements like humidity, temperature ranges, and exposure to elements necessitate careful consideration during equipment selection and deployment.
Furthermore, terrain characteristics influence machine adaptability and maintenance needs, influencing decisions regarding suitability and operational effectiveness. Assessing these factors ensures optimal performance and durability amidst diverse environmental challenges.
Highlight how environmental conditions such as space limitations, temperature variations, and safety regulations influence machine selection.
In the realm of machine procurement, the choice of equipment hinges significantly on the environmental context. Factors like spatial constraints, fluctuations in temperature, and adherence to safety protocols wield substantial influence over the suitability of machinery for specific tasks.
Space limitations necessitate compact designs or adaptable configurations, ensuring seamless integration into confined work areas. Temperature variations mandate machinery capable of withstanding diverse climate conditions without compromising performance or durability.
Safety regulations further dictate the design and operational parameters of machines, demanding features that mitigate risks and ensure compliance with established standards. Consequently, a meticulous assessment of these environmental factors is indispensable in selecting machines that not only meet operational needs but also endure and excel within their designated settings.
This HTML-formatted section highlights how environmental conditions shape the selection of machinery, using synonyms as requested.
Choosing the Right Machine Size
When selecting the optimal equipment dimensions, it’s crucial to align the machine’s proportions with the specific operational requirements. This decision influences performance efficiency and overall productivity. Here, we delve into the strategic factors guiding the selection process, ensuring harmonious integration with operational needs.
- Consider Operational Scope
- Evaluate Performance Parameters
- Assess Spatial Constraints
- Factor in Longevity and Maintenance
Each criterion plays a pivotal role in determining the appropriate scale of machinery, steering towards optimal functionality within diverse operational environments. By integrating these considerations, stakeholders can secure a tailored solution that maximizes operational efficacy and resource utilization.
Optimizing Performance Efficiency
In this section, we delve into enhancing the operational effectiveness and maximizing output productivity. Achieving peak performance involves fine-tuning operational processes to streamline workflow and elevate overall efficiency. By refining operational strategies and leveraging optimal methodologies, organizations can ensure heightened performance levels and improved output quality. This segment explores effective techniques to boost operational efficiency, focusing on optimizing workflow dynamics and enhancing output efficacy through strategic enhancements.
- Implementing streamlined procedures to enhance workflow dynamics
- Maximizing output quality through strategic enhancements
- Focusing on efficiency metrics to gauge operational effectiveness
- Refining methodologies to elevate overall performance
- Utilizing advanced strategies for improved operational outcomes
Explain how selecting the appropriate machine dimensions enhances efficiency and decreases operational expenses over time.
Choosing the right machine size plays a pivotal role in optimizing productivity and minimizing costs in the long run. When you carefully evaluate the dimensions of the equipment to suit the specific needs of your tasks, you ensure that operations flow smoothly without unnecessary downtime or inefficiencies. This strategic approach not only boosts output but also contributes to cost savings by reducing maintenance requirements and energy consumption.
Moreover, the proper dimensions contribute to operational agility, allowing your team to adapt swiftly to changing demands without compromising on performance. By investing in machines that are appropriately sized for the workload and operational environment, businesses can achieve sustainable growth and maintain competitive advantages in their respective industries.
This HTML-formatted section explains how selecting the right machine size enhances productivity and reduces operational costs over time, following your specifications.