The Importance of Quality Control in Selling Iron for Your Business
Quality control in iron products manufacturing: Importance, techniques, and benefits for businesses
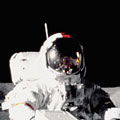
- Anthony Arphan
- 35 min read
Amidst the ever-evolving landscape of commerce, where competition reigns and success lies in the hands of meticulous decision-making, it becomes increasingly paramount to recognize the significance of guaranteeing excellence in the production and distribution of your valuable metal products. For those immersed in the industry of forging prosperity through the sale of durable metallic materials, there is an intricate dance between appeasing consumer demands and securing long-term business sustainability.
With the world revolving around a myriad of options, customers are no longer enthralled merely by the notion of “what” is being offered, but rather, they demand accountability for the “how” and “why” behind the creation of their coveted possessions. This necessitates the implementation of comprehensive quality assurance practices that stretch beyond surface-level considerations, penetrating deep into the very essence of your merchandise’s journey from inception to the hands of consumers.
Within the vast realm of metal commerce, the pursuit of quality control emerges as a beacon of heightened assurance for both business owners and their clientele. The steerage of this ship is contingent upon a well-crafted framework encompassing meticulous inspections, regulatory compliance, and consistent oversight. By engendering a culture of meticulousness and stringent adherence to rigorous quality checks, business owners can become guardians of their customers’ trust and maintain an indomitable presence in the market.
The Importance of Quality Control
In today’s competitive market, ensuring that the products you sell meet the highest standards is essential for the success of your business. The significance of quality control cannot be overstated, as it directly affects customer satisfaction, reputation, and ultimately, the overall profitability of the company.
Quality control encompasses a set of processes and procedures that are implemented to monitor and maintain the excellence of products. It involves a series of checks and inspections, ensuring that each item meets the specified criteria, be it durability, functionality, or performance.
By consistently enforcing quality control measures, you demonstrate a commitment to delivering superior products to your customers. In doing so, you build trust and loyalty, as customers appreciate the reliability and dependability of your offerings.
Moreover, quality control helps you identify and eliminate any defects or flaws in the manufacturing process. This not only boosts the efficiency of your operations but also reduces costs associated with repairs, returns, and customer complaints.
Furthermore, quality control aids in maintaining regulatory compliance and adherence to industry standards. It ensures that your products meet the required safety and quality regulations, protecting both your customers and your business from potential legal issues.
In summary, the importance of quality control cannot be emphasized enough. It serves as the foundation for successful businesses, contributing to customer satisfaction, brand reputation, and long-term profitability. By investing in robust quality control measures, you can differentiate yourself from competitors and secure a loyal customer base.
Enhancing Customer Satisfaction
Creating a positive experience for your customers is instrumental in building a successful business. By prioritizing customer satisfaction, businesses can foster loyalty, gain a competitive edge, and foster long-term relationships with their clientele.
One key aspect of enhancing customer satisfaction is ensuring consistent product quality. When customers receive products that meet or exceed their expectations, they feel valued and confident in their purchase decision. Employing rigorous quality control measures throughout the manufacturing process enables businesses to deliver reliable and durable iron products to their customers.
In addition to product quality, effective communication plays a vital role in enhancing customer satisfaction. Prompt and informative responses to customer inquiries, concerns, or feedback demonstrate a commitment to their needs. Clear and helpful communication not only resolves any issues but also builds trust and fosters positive customer relationships.
Gaining insights into customer preferences and expectations is another strategy to enhance customer satisfaction. Through surveys, feedback forms, or customer reviews, businesses can gather valuable information about their customers’ preferences, enabling them to tailor their products and services accordingly. By actively incorporating customer feedback into their decision-making processes, businesses can ensure customer-centricity and improve overall customer satisfaction.
Going above and beyond to provide exceptional customer service is yet another way to enhance customer satisfaction. Training and empowering employees to deliver personalized, attentive, and friendly service can leave a lasting positive impression on customers. Whether it’s through addressing their needs, providing expert advice, or handling any concerns promptly and efficiently, outstanding customer service creates a memorable experience and fosters customer loyalty.
In conclusion, enhancing customer satisfaction is crucial for businesses in the iron industry. By prioritizing product quality, effective communication, understanding customer preferences, and delivering exceptional customer service, businesses can cultivate strong customer relationships and differentiate themselves in the competitive market.
Maintaining Brand Reputation
Ensuring the integrity of your brand and its reputation is of utmost importance in the competitive business landscape. It is vital to establish and maintain strong brand recognition, trust, and loyalty among consumers. This can be achieved through a comprehensive approach to quality control, which involves implementing stringent measures to meet or exceed customer expectations.
A key aspect of maintaining brand reputation is consistently delivering high-quality products to customers. Quality control plays a pivotal role in ensuring that every item that bears your brand name meets the highest standards of durability, reliability, and performance. By investing in robust quality control processes, you can minimize the risk of product defects, prevent recalls, and uphold the reputation of your brand as a provider of dependable and superior goods.
Moreover, a strong brand reputation is built on the foundation of exceptional customer service. Every interaction with your customers should be handled with care, ensuring their satisfaction and resolving any concerns promptly and efficiently. By going above and beyond to provide excellent service, you can reinforce positive brand associations and foster long-term relationships with your customers.
Another critical aspect of maintaining brand reputation is actively monitoring and addressing customer feedback. Regularly collect insights, both positive and negative, from various channels such as social media, online reviews, and surveys. Analyze this feedback to identify recurring issues or patterns and take immediate action to rectify any shortcomings. By demonstrating responsiveness and a commitment to continuous improvement, you can strengthen your brand’s credibility and build trust with your audience.
Furthermore, maintaining open and transparent communication with your customers is essential for preserving brand reputation. Keep them informed about any updates, improvements, or new product launches to showcase your brand’s dedication to innovation and delivering value. By engaging with your customers through various communication channels, you can foster a sense of community and loyalty.
Benefits of Maintaining Brand Reputation |
---|
Enhances customer trust and loyalty |
Positions your brand as a leader in the industry |
Increases customer retention and advocacy |
Attracts new customers through positive word-of-mouth |
Provides a competitive edge in the market |
In conclusion, maintaining brand reputation is a critical aspect of running a successful business. By prioritizing quality control, delivering excellent customer service, actively monitoring feedback, and engaging in transparent communication, you can establish and safeguard your brand’s reputation, gaining a competitive advantage in the market.
Ensuring Product Reliability
When it comes to the success of your business, ensuring the reliability of your products is of utmost importance. Without reliable products, it can be difficult to build trust with your customers and maintain a strong reputation in the industry. In this section, we will explore the various steps you can take to guarantee the dependability of your products.
Thorough Testing: One of the key methods to ensure product reliability is through thorough testing. This involves subjecting your products to a series of rigorous tests to identify any potential weaknesses or flaws. By conducting tests under various conditions and scenarios, you can gain valuable insights into the performance and durability of your products.
Quality Materials: The use of high-quality materials is essential for creating reliable products. By sourcing materials from trusted suppliers and conducting thorough inspections, you can ensure that your products are built to last. This includes using durable metals, such as steel or alloy, that can withstand the demands of everyday use.
Stringent Manufacturing Processes: Implementing stringent manufacturing processes is crucial for maintaining product reliability. This involves adhering to strict quality control measures throughout the production cycle. By closely monitoring each stage of manufacturing, you can minimize the risk of defects and inconsistencies in your products.
Ongoing Evaluation: Product reliability is not a one-time achievement. It requires ongoing evaluation and improvement. By continually assessing customer feedback, conducting market research, and staying up-to-date with industry advancements, you can identify areas for improvement and implement necessary changes to enhance the reliability of your products.
Effective Communication: Communication plays a vital role in ensuring product reliability. It is important to establish clear lines of communication between different teams within your business, as well as with suppliers and customers. This enables timely sharing of information and ensures that everyone is on the same page regarding product specifications and requirements.
In conclusion, product reliability is a cornerstone of any successful business. By investing in thorough testing, using quality materials, implementing stringent manufacturing processes, conducting ongoing evaluation, and maintaining effective communication, you can build a reputation for delivering dependable products to your customers.
Cost Savings through Quality Control
Enhancing your bottom line and improving business efficiency can be achieved through the implementation of robust quality control measures. By ensuring the consistency and reliability of your products or services, quality control can lead to significant cost savings and an enhanced reputation in the market.
Implementing effective quality control measures can minimize the risk of defective products or services reaching your customers. This, in turn, reduces the potential costs associated with recalls, repairs, and customer complaints. By identifying and addressing quality issues at their source, businesses can avoid the financial repercussions of product failures or service failures, ultimately saving money in the long run.
Furthermore, quality control can also lead to cost reductions by streamlining business processes. By carefully monitoring and analyzing the production or service delivery process, businesses can identify inefficiencies, eliminate waste, and optimize resource allocation. This improved efficiency not only reduces costs but also enhances productivity and profitability.
Investing in quality control can also have a positive impact on customer satisfaction and loyalty. By consistently delivering high-quality products or services, businesses can build a reputation as a reliable and trusted provider. Satisfied customers are more likely to become repeat customers and recommend the business to others, leading to increased sales and revenue.
Overall, implementing effective quality control measures can have a profound impact on a business’s financial performance. By avoiding the costs associated with product or service failures, optimizing business processes, and enhancing customer satisfaction, businesses can achieve significant cost savings and create a competitive advantage in the market.
Reducing Rework and Scrap
Minimizing the need for redoing work and minimizing waste are two essential factors for ensuring operational efficiency and maximizing profits. By implementing effective quality control measures, businesses can significantly reduce the occurrence of rework and scrap, leading to improved productivity and cost savings.
One key aspect of reducing rework and scrap is identifying potential issues early on in the production process. By conducting thorough inspections and tests at various stages, businesses can identify any deviations from the desired quality standards and take immediate corrective actions. This proactive approach helps prevent defects from propagating further down the line, minimizing the need for extensive rework.
Implementing robust quality control systems also involves fostering a culture of continuous improvement within the organization. Encouraging employees to take ownership of their work and providing them with the necessary training and resources to understand and implement quality standards can go a long way in reducing rework and scrap. Regular performance evaluations and feedback can help identify areas for improvement and enable employees to strive for excellence.
Utilizing efficient production techniques and modern technology can also contribute to reducing rework and scrap. Adopting automated systems and equipment can minimize human errors and improve precision in manufacturing processes. Additionally, monitoring production data in real-time and analyzing it for potential quality issues can help in identifying and rectifying deviations promptly.
Another crucial aspect of reducing rework and scrap is establishing clear communication channels and documentation processes. Effective communication between different departments and stakeholders involved in the production process ensures that everyone is aware of the quality requirements and any changes or updates. Detailed documentation of processes, procedures, and quality standards helps in maintaining consistency and provides a reference for troubleshooting and identifying potential problem areas.
- Identify potential issues early on through thorough inspections and tests.
- Encourage a culture of continuous improvement and employee ownership.
- Utilize efficient production techniques and modern technology.
- Establish clear communication channels and documentation processes.
By implementing these strategies, businesses can optimize their operations, minimize rework and scrap, and ensure the delivery of high-quality products, ultimately strengthening their position in the market.
Minimizing Customer Returns
Reducing product returns is a critical aspect of any business strategy, particularly when it comes to selling iron. Ensuring customer satisfaction and minimizing the number of returns can have a significant impact on the success and profitability of your business. In this section, we will explore several effective strategies to help you minimize customer returns and enhance your overall business operations.
- Thorough product inspections: One of the primary reasons for customer returns is receiving faulty or damaged iron. Implementing a rigorous quality control process to thoroughly inspect each iron product before it reaches the customer is paramount. This includes checking for any defects, damages, or inconsistencies in the material or construction.
- Accurate product descriptions: Clear and accurate product descriptions play a crucial role in minimizing customer returns. Providing detailed information about the iron’s specifications, dimensions, features, and limitations can help customers make informed purchasing decisions. This reduces the likelihood of them receiving a product that doesn’t meet their expectations.
- Expedited shipping and delivery: Timely delivery is essential in maintaining customer satisfaction. Delayed or mishandled shipments can result in a higher number of returns. Collaboration with reliable shipping partners and implementing efficient tracking systems can minimize shipping-related issues and ensure prompt delivery of the iron products to customers.
- Effective customer support: Offering exceptional customer support can significantly reduce returns. Provide timely and knowledgeable assistance to customers who have queries or concerns about the iron they purchased. Addressing their issues promptly and providing appropriate solutions can help prevent returns resulting from misunderstandings or dissatisfaction.
- Customer feedback and reviews: Encouraging customers to leave feedback and reviews after purchasing your iron products can provide valuable insights. Analyzing this feedback can help identify areas for improvement and make necessary changes to reduce future returns. Additionally, positive reviews can help attract more customers and increase overall trust in the quality of your iron.
By implementing these practices and continuously monitoring and improving your operations, you can minimize customer returns, enhance customer satisfaction, and ensure the long-term success of your iron-selling business.
Quality Control in the Manufacturing Process
In today’s competitive business landscape, ensuring the utmost quality of manufactured goods has become an essential aspect of success. It is imperative for businesses to implement robust quality control measures throughout the entire manufacturing process. By doing so, companies can guarantee that their products meet or exceed customer expectations, ensuring customer satisfaction and loyalty.
Effective quality control in the manufacturing process involves a systematic approach to identify and rectify any potential defects or issues that may arise during production. This process necessitates a keen attention to detail and a commitment to maintaining high standards at every stage, from the sourcing of raw materials to the final assembly of the product.
Inspection and testing play a pivotal role in quality control. Regular inspections help to identify any deviations from specified quality standards, enabling prompt corrective actions. Additionally, comprehensive testing ensures that products meet all necessary criteria, such as performance, durability, and safety. By diligently conducting inspections and testing throughout the manufacturing process, businesses can mitigate the risk of product failures and recalls.
The establishment of quality control checkpoints is another crucial aspect of maintaining high standards. These checkpoints, strategically placed at various stages of the production process, allow for continual monitoring and evaluation. By closely monitoring quality control checkpoints, manufacturers can promptly address any issues or non-conformities, thereby minimizing the likelihood of defective products reaching the market.
Employee training and competence are integral to achieving consistent quality control. By training employees on best practices, quality standards, and product specifications, businesses can enhance their workforce’s skills and knowledge. Employees who are competent in their roles and understand the importance of quality control can actively contribute to the prevention and resolution of quality issues.
Implementing a quality control culture throughout the organization is equally vital. This involves fostering an environment where every employee takes responsibility for the quality of their work and is committed to upholding high standards. A strong quality control culture promotes continuous improvement, innovation, and a customer-centric approach.
In conclusion, quality control in the manufacturing process is a fundamental aspect of business success. By implementing robust quality control measures, conducting thorough inspections and testing, establishing checkpoints, investing in employee training, and fostering a quality control culture, businesses can ensure the production of high-quality products that meet or exceed customer expectations.
Setting Standards and Specifications
Establishing and defining standards and specifications is an essential aspect in ensuring the quality and integrity of the iron products you sell. These guidelines serve as a reference point for evaluating the excellence and consistency of your goods, allowing you to meet the expectations and demands of your customers. By implementing effective standards and specifications, you can guarantee that your business maintains a strong reputation for providing reliable and superior iron products.
Defining Parameters for Quality:
When it comes to selling iron, setting specific standards and specifications helps in determining the quality parameters that your products must meet. These guidelines outline the attributes, features, and characteristics that a particular iron product should possess in order to be considered as meeting the specified quality. By defining these parameters, you can ensure that your customers receive products that meet their expectations and deliver the intended performance.
Ensuring Consistency and Uniformity:
Setting standards and specifications also plays a significant role in maintaining consistency and uniformity in the iron products you sell. By establishing clear guidelines, you create a framework for manufacturing and production processes that facilitates the control and monitoring of each stage. This ensures that every product meets the defined standards, leading to consistent quality across all your offerings. Consistency and uniformity are vital for building customer trust and loyalty, as they provide assurance that your products will always meet their desired performance and durability.
Meeting Legal and Regulatory Requirements:
Another crucial aspect of setting standards and specifications is ensuring compliance with legal and regulatory requirements. These guidelines ensure that your iron products adhere to the safety and quality standards mandated by relevant authorities. By aligning your products with these requirements, you demonstrate your commitment to conducting business ethically and responsibly. This, in turn, enhances your reputation and credibility among customers, suppliers, and other stakeholders in the industry.
Promoting Continuous Improvement:
Standards and specifications are not static; they should be seen as a foundation for continuous improvement. By regularly reviewing and updating your guidelines, you can adapt to changing market trends, technological advancements, and customer preferences. This commitment to improvement ensures that your iron products evolve alongside the industry and remain competitive. Additionally, it allows you to proactively address any gaps or areas of improvement, further enhancing the quality and value of your offerings.
In conclusion, setting and adhering to standards and specifications is crucial for any business involved in selling iron. These guidelines help define quality parameters, maintain consistency, ensure compliance, and drive continuous improvement. By prioritizing the establishment and implementation of effective standards and specifications, your business can thrive in delivering high-quality iron products that meet the demands of your customers and surpass their expectations.
Conducting Inspections and Tests
Ensuring the quality of iron products is essential for any business involved in selling these materials. To maintain customer satisfaction and enhance the overall reputation of your company, conducting regular inspections and tests is crucial. These procedures enable you to identify any potential issues or defects in the iron, guaranteeing that only high-quality materials are delivered to your clients.
In order to conduct effective inspections and tests, it is important to establish clear guidelines and protocols. This includes defining specific standards and specifications that the iron products must meet. By doing so, you create a framework for evaluating the quality of the materials and ensure consistency in the inspection process.
- Visual Inspections: One of the initial steps in quality control involves visually examining the iron products. This allows inspectors to detect any visible defects such as scratches, dents, or discoloration. Inspectors should be trained to identify these imperfections and promptly address them.
- Dimensional Checks: Accurate measurements are crucial to verifying the compliance of iron products with the required specifications. Through dimensional checks, inspectors can ensure that the dimensions of the iron pieces align with the predetermined standards. This helps guarantee that the products will fit properly and function as intended.
- Material Analysis: Conducting various tests to analyze the properties of the iron is essential in quality control. These tests include hardness tests, tensile strength tests, and corrosion resistance tests. By assessing the material’s characteristics, you can determine its durability and suitability for the intended application.
- Functional Testing: To ensure that the iron products perform as expected, functional testing is necessary. This involves subjecting the materials to simulated or real-life conditions to assess their performance, functionality, and reliability. Functional tests may include load testing, stress testing, and endurance testing.
Furthermore, it is important to establish an effective documentation system to record all inspection and test results. This allows you to track the quality of your iron products over time and provides a valuable reference in case of any disputes or issues. Regularly reviewing and analyzing this data can help identify any patterns or recurring problems, enabling you to take proactive measures to improve product quality.
In conclusion, conducting thorough inspections and tests is crucial for ensuring the quality and reliability of the iron products your business sells. By implementing clear guidelines, utilizing various inspection methods, and maintaining comprehensive documentation, you can continuously improve the quality control process and enhance customer satisfaction.
Implementing Corrective Actions
In order to ensure the optimal quality and performance of your products, it is essential to have a robust system in place for implementing corrective actions. These actions are necessary to address any deviations or shortcomings identified through quality control processes.
The implementation of corrective actions involves a systematic approach to identifying the root causes of quality issues and developing appropriate solutions. It requires thorough analysis of the underlying factors contributing to the problem, such as manufacturing processes, raw materials, or equipment malfunction. Once the root causes have been determined, effective and targeted corrective actions can be implemented to prevent future occurrences.
A key aspect of implementing corrective actions is the establishment of clear and achievable objectives. These objectives should be measurable and time-bound, enabling the progress and effectiveness of the actions to be monitored and evaluated. It is also important to assign responsibilities and roles to individuals or teams who will be responsible for carrying out the corrective actions and tracking their outcomes.
The use of data and data analysis techniques is crucial in the implementation of corrective actions. By analyzing relevant data, such as production records or customer feedback, patterns and trends can be identified, helping to pinpoint areas where improvements are needed. This data-driven approach allows for evidence-based decision making and ensures that corrective actions are precisely targeted to address the root causes of quality issues.
Regular review and assessment of the implemented corrective actions is vital to ensuring their effectiveness and identifying any further improvements that may be required. This includes collecting and analyzing data on the performance of the corrective actions and evaluating their impact on product quality and customer satisfaction. Continuous improvement should be an ongoing process, with a commitment to refining and enhancing the corrective measures to achieve optimal results.
Key Steps in Implementing Corrective Actions |
---|
1. Identify the root causes of quality issues. |
2. Develop clear and measurable objectives. |
3. Assign responsibilities and roles. |
4. Utilize data and data analysis techniques. |
5. Regularly review and assess the implemented actions. |
Quality Control Techniques
Ensuring the consistent quality of your iron products is paramount for the success of your business. Without effective quality control techniques, your reputation, customer satisfaction, and overall business performance may suffer. In this section, we will explore various strategies and methods you can employ to maintain high-quality standards and meet customer expectations.
- Statistical Process Control (SPC):
Implementing SPC techniques allows you to monitor and control the quality of your iron products throughout the manufacturing process. By collecting and analyzing data, you can identify and address any variations or deviations that may occur, ensuring consistent quality output.
- Failure Mode and Effects Analysis (FMEA):
FMEA is a structured approach that helps you proactively identify and mitigate potential failures or defects in your iron products. By systematically analyzing the various failure modes and their potential effects, you can take preventive measures to avoid quality issues and improve product reliability.
- Six Sigma:
Adopting Six Sigma methodology enables you to achieve a high level of quality by reducing process variation and minimizing defects. This data-driven approach focuses on continuous improvement, utilizing statistical analysis and problem-solving tools to enhance the efficiency and effectiveness of your manufacturing processes.
- Total Quality Management (TQM):
TQM is a comprehensive management approach that emphasizes quality as a core organizational value. By involving all employees in the quality improvement process and encouraging a culture of continuous learning and innovation, TQM aims to enhance customer satisfaction and drive business success.
- Supplier Quality Management:
Establishing a robust supplier quality management system is crucial to ensuring the quality of raw materials and components used in your iron products. Conducting regular audits, setting stringent quality standards, and fostering strong relationships with reliable suppliers can help maintain consistency in the quality of your final products.
- Quality Inspections and Testing:
Regular inspections and testing at various stages of the manufacturing process are essential for identifying any deviations from quality standards. From raw material inspection to in-process testing and final product evaluation, implementing rigorous quality checks helps identify and rectify any issues that may impact product quality.
By implementing these quality control techniques, you can not only enhance the quality of your iron products but also instill confidence in your customers and gain a competitive edge in the market. Prioritizing quality control will undoubtedly contribute to the long-term success and sustainability of your business.
Statistical Process Control
In the pursuit of optimizing productivity and ensuring consistent product quality, businesses must turn to statistical process control (SPC) methodologies. SPC provides a systematic approach for monitoring and controlling the manufacturing process, reducing waste, and enhancing overall efficiency.
SPC involves the collection and analysis of data obtained at various stages of the production process. By using statistical techniques, businesses can identify patterns, trends, and deviations from the desired specifications. This enables them to make informed decisions and take corrective actions to improve quality.
One of the key benefits of SPC is its ability to detect and prevent defects before they occur, thereby reducing the likelihood of producing non-conforming products. Additionally, SPC allows for the identification of process variations and the implementation of measures to minimize these variations, leading to greater consistency in product quality.
Implementing SPC involves establishing control charts to visually represent the performance of the manufacturing process over time. These charts provide a graphical representation of data collected from the production line, highlighting any deviations from the desired target values. By monitoring these charts in real-time, businesses can quickly identify anomalies and initiate prompt corrective actions.
Furthermore, SPC can also be used to monitor the capability of the process, determining whether it is capable of consistently producing products within the required specifications. By analyzing process capability indices, businesses can assess the potential risks associated with variations in the manufacturing process and take proactive measures to mitigate them.
In conclusion, statistical process control plays a vital role in maintaining quality control in businesses. By implementing SPC methodologies, companies can optimize their production processes, minimize defects, and enhance customer satisfaction without compromising efficiency. Utilizing this data-driven approach empowers businesses to consistently deliver high-quality products, thereby gaining a competitive edge in the industry.
Six Sigma Approach
The Six Sigma approach is a highly effective methodology that emphasizes the importance of minimizing defects and errors in business processes. By implementing this approach, companies can enhance their quality control measures and achieve significant improvements in their overall operations.
1. Focus on Continuous Improvement
One of the key principles of the Six Sigma approach is continuous improvement. It encourages businesses to continually evaluate and optimize their processes to reduce defects and errors. Through the systematic use of statistical analysis, companies can identify areas of improvement and implement strategies to achieve higher levels of quality.
2. Data-Driven Decision Making
The Six Sigma approach relies heavily on data-driven decision making. By gathering and analyzing data, businesses can gain valuable insights into their processes and identify potential areas of improvement. This information enables them to make informed decisions and implement effective solutions based on facts and figures.
3. Defect Reduction and Standardization
The primary goal of the Six Sigma approach is to reduce defects and achieve process standardization. By implementing effective quality control measures and eliminating variations in processes, businesses can ensure consistent and high-quality products. This not only improves customer satisfaction but also helps in building a strong reputation for the business.
4. Emphasis on Training and Certifications
The Six Sigma approach recognizes the importance of specialized training and certifications. It encourages businesses to invest in training their employees in Six Sigma methodologies and techniques. By equipping employees with the necessary skills and knowledge, companies can develop a culture of continuous improvement and ensure the successful implementation of quality control measures.
5. Customer-Centric Approach
The Six Sigma approach places a strong emphasis on meeting customer expectations and requirements. By understanding the needs and preferences of customers, businesses can align their processes accordingly and deliver products that consistently meet or exceed customer expectations. This customer-centric approach is crucial for long-term success and customer retention.
6. Process Optimization and Waste Reduction
The Six Sigma approach encourages businesses to optimize their processes to eliminate waste and inefficiency. By identifying and eliminating non-value added activities, businesses can streamline their operations and improve productivity. This not only increases profitability but also enhances the overall quality of products and services provided.
In conclusion, the Six Sigma approach is a powerful tool for businesses to achieve excellence in their quality control measures. By focusing on continuous improvement, data-driven decision making, defect reduction, training and certifications, customer-centricity, and process optimization, companies can enhance their overall operations and ensure the delivery of high-quality products and services.
Quality Control Tools and Technologies
In the pursuit of excellence and customer satisfaction, it is imperative for businesses to implement effective quality control measures. Quality control tools and technologies play a vital role in ensuring the consistency and reliability of products in the competitive market. These tools and technologies encompass a range of methodologies and systems that enable businesses to identify, monitor, and rectify any deviations or defects in their manufacturing processes.
Statistical Process Control (SPC) is one of the fundamental tools used in quality control. It involves the collection and analysis of data to identify variations and trends in the manufacturing process. By utilizing statistical techniques, businesses can make informed decisions to improve the overall quality of their products and minimize defects.
Fault Tree Analysis (FTA) is another valuable tool that assists in identifying potential failure points within a system. This method helps businesses to systematically analyze the various factors that may contribute to product failures. By mapping out these factors, businesses can develop effective preventive measures and mitigate risks, thereby enhancing product quality and reliability.
Six Sigma is a comprehensive and structured approach used by businesses to improve process efficiency and minimize defects. By employing a statistical methodology and implementing data-driven strategies, Six Sigma aims to reduce variations and achieve near-perfect quality levels. This powerful technique helps businesses maintain consistent quality standards, enhance customer satisfaction, and ultimately increase their market competitiveness.
Lean Manufacturing principles also play a crucial role in quality control. By eliminating waste, streamlining processes, and continuously improving operations, businesses can enhance overall product quality. Lean Manufacturing encourages a culture of continuous improvement and focuses on maximizing value for the customer while minimizing defects, reducing costs, and increasing productivity.
Automation and Technology have revolutionized the field of quality control. Advanced technologies such as robotics, artificial intelligence, and machine learning enable businesses to automate various stages of quality control, including inspection, testing, and data analysis. These technologies not only improve the accuracy and speed of quality control processes but also reduce human error and ensure consistent adherence to quality standards.
In conclusion, implementing the right quality control tools and technologies is vital for businesses to maintain a competitive edge in the market. By utilizing statistical analysis, fault tree analysis, techniques like Six Sigma, lean manufacturing principles, and harnessing the power of automation and technology, businesses can achieve consistent and high-quality products, enhance customer satisfaction, and drive business growth.
Inspection Equipment
In order to maintain the high standards and ensure the quality of your products, it is essential to invest in reliable and efficient inspection equipment. These tools play a crucial role in the manufacturing process, as they allow you to identify any potential defects or irregularities in your iron products. By utilizing advanced technology and innovative techniques, inspection equipment enables you to uphold excellence, enhance customer satisfaction, and safeguard the reputation of your business.
Various types of inspection equipment are available on the market, offering different capabilities and features tailored to the specific needs of your iron-selling business. From non-destructive testing instruments to inline quality control systems, these tools help you detect flaws, measure dimensions, and assess the overall integrity of your iron products.
One commonly used inspection equipment is the ultrasonic testing device. This non-destructive technique uses high-frequency sound waves to detect internal defects in iron, such as cracks, voids, or inclusions. By analyzing the reflected waves, the equipment provides accurate information about the internal structure and integrity of the iron, allowing you to identify any potential weaknesses that may affect the quality and performance of your products.
Another crucial type of inspection equipment is the coordinate measuring machine (CMM). This precision tool employs a probe that measures the dimensions and geometry of your iron products, ensuring they meet the required specifications. With its ability to accurately assess complex shapes and surfaces, the CMM helps you guarantee that your iron pieces are within tolerance, eliminating the risk of manufacturing defects and customer dissatisfaction.
In addition to these specific examples, there is a wide range of inspection equipment available, each serving a unique purpose in quality control. X-ray machines, optical comparators, and surface roughness testers are just a few examples of the diverse tools that can be utilized to enhance the inspection process, further ensuring the quality and reliability of your iron products.
Investing in inspection equipment demonstrates your commitment to producing high-quality iron products, while also promoting efficiency and cost-effectiveness in your business operations. By implementing rigorous quality control measures and utilizing advanced inspection tools, you can differentiate yourself from competitors and build a strong reputation for reliability, ultimately driving your business towards long-term success.
Data Analysis Software
In the realm of business operations, the utilization of data analysis software plays a pivotal role in gaining valuable insights and making informed decisions. This section explores the significance of employing advanced software tools for analyzing data and highlights the numerous benefits it can bring to a business.
Effective data analysis software enables businesses to harness the power of data by collecting, organizing, and interpreting it in a meaningful way. By utilizing these software tools, companies can dive deep into their operational data, uncover intriguing patterns, and extract actionable knowledge. This empowers decision-makers to understand market trends, identify customer preferences, and optimize their strategies accordingly.
Furthermore, data analysis software provides businesses with the ability to examine vast datasets from multiple sources, allowing for comprehensive analysis and more accurate results. With the aid of sophisticated algorithms and statistical techniques, these software tools facilitate the identification of correlations, outliers, and significant trends that might otherwise go unnoticed. This enables businesses to make data-driven decisions and be more competitive in their respective industries.
One of the key advantages of data analysis software is its ability to automate and streamline analytical processes. By automating repetitive tasks, such as data cleaning and transformation, these tools significantly reduce the time and effort required for analysis. This allows businesses to focus on interpreting the results and deriving meaningful insights, rather than spending excessive time on manual data processing.
Data analysis software also enhances collaboration among teams by providing a centralized platform for data sharing and analysis. It allows multiple stakeholders to access and work on the same dataset simultaneously, facilitating collaboration and improving efficiency. Additionally, these software tools often offer interactive visualizations and customizable dashboards, enabling users to communicate findings effectively and present data-driven recommendations.
Benefits of Data Analysis Software: |
---|
1. Enhanced decision-making capabilities |
2. Improved understanding of market trends |
3. Optimization of business strategies |
4. Accurate identification of correlations and outliers |
5. Automation of repetitive analytical tasks |
6. Streamlined data processing |
7. Facilitation of collaboration and efficient data sharing |
8. Effective communication of findings through visualizations |
Quality Control in Supply Chain Management
Ensuring top-notch quality of products is of utmost importance in the management of supply chains. By implementing effective quality control measures, businesses can guarantee that their products meet the highest standards and fulfill customer expectations. Quality control serves as a critical component in the overall functioning of supply chains, ensuring the smooth flow of goods from manufacturers to end consumers.
Effective quality control practices involve monitoring and assessing every stage of the supply chain. This includes evaluating the quality of raw materials, scrutinizing production processes, inspecting finished products, and conducting rigorous quality tests. By conducting thorough inspections and tests at various points in the supply chain, businesses can detect and rectify any potential quality issues promptly.
Quality control also plays a significant role in enhancing customer satisfaction and loyalty. By consistently delivering products that meet or exceed customers’ expectations, businesses can build a positive reputation in the market. Additionally, effective quality control measures can minimize the occurrence of defects and errors, reducing the risk of product recalls or customer complaints.
Implementing quality control in supply chain management offers numerous benefits for businesses. It helps in optimizing production processes, reducing costs, and maximizing operational efficiency. By identifying and addressing quality issues early on, businesses can minimize wastage and rework, thereby improving overall productivity and profitability.
Furthermore, quality control contributes to fostering strong relationships with suppliers. By setting stringent quality standards and collaborating closely with suppliers, businesses can ensure that only high-quality materials are used in the production process. This not only enhances the quality of the final product but also strengthens the reliability and trustworthiness of the entire supply chain.
In conclusion, quality control acts as a cornerstone in supply chain management, enabling businesses to maintain consistent quality, gain a competitive edge, and drive customer satisfaction. By prioritizing quality control measures, businesses can uphold their reputation, enhance operational efficiency, and ensure the long-term success of their ventures.
Selecting Reliable Suppliers
When it comes to running a successful business, choosing dependable and trustworthy suppliers is paramount. The suppliers you choose can directly impact the quality and success of your products. Therefore, it is crucial that you carefully consider a variety of factors before making a decision.
Establishing Quality Agreements
Clearly defining and ensuring the quality of the iron products you sell is essential for the success and reputation of your business. In order to achieve this, it is crucial to establish quality agreements with your suppliers and manufacturers.
Quality agreements serve as a legal document between your business and your suppliers, outlining the specifications, requirements, and expectations regarding the quality of the iron products. These agreements help to ensure a consistent and reliable supply of high-quality iron, ultimately leading to customer satisfaction and loyalty.
When establishing quality agreements, it is important to communicate your business’s quality standards clearly and precisely. This includes defining the desired physical characteristics, such as the strength, durability, and composition of the iron. It also involves specifying any required certifications, such as ISO standards, that the suppliers and manufacturers should meet.
Additionally, it is important to include provisions for regular inspections and audits to verify the quality of the iron products. This could involve random sampling and testing conducted by a qualified third-party, as well as thorough monitoring of the manufacturing processes and quality control measures implemented by your suppliers.
By establishing quality agreements, you can proactively address any potential quality issues and maintain consistent product quality throughout your supply chain. This not only helps to prevent defects and customer complaints but also builds a reputation for your business as a reliable supplier of high-quality iron products.
Ultimately, investing time and effort into establishing quality agreements with your suppliers and manufacturers can contribute to the long-term success and growth of your business. It demonstrates your commitment to delivering superior products to your customers and differentiates you from competitors who may overlook the importance of quality control in the selling of iron products.
Benefits of Implementing Quality Control
When it comes to ensuring the success and growth of your business, one cannot underestimate the importance of implementing effective quality control measures. By maintaining strict standards and processes, businesses can benefit in numerous ways, ultimately leading to improved customer satisfaction, increased profitability, and enhanced brand reputation.
Enhanced Customer Satisfaction: Implementing quality control measures ensures that the products you deliver to your customers meet or exceed their expectations. Consistently providing high-quality products that are free from defects or deficiencies will not only satisfy your customers but also build trust and loyalty towards your brand.
Increased Profitability: Quality control helps to reduce the number of defective products, minimizing the need for recalls, repairs, or customer returns. By minimizing waste and improving production efficiency, businesses can save both time and money, ultimately leading to increased profitability.
Improved Brand Reputation: A strong commitment to quality control establishes your business as a reliable and trustworthy provider within the industry. Word-of-mouth referrals and positive customer reviews can significantly contribute to the growth of your brand reputation, attracting new customers and opportunities for expansion.
Lower Costs: Implementing quality control measures helps businesses identify inefficiencies, defects, and non-compliance issues early in the production process. By addressing these issues promptly, businesses can avoid costly rework, scrap, or additional expenses associated with product failures or non-compliance with regulations.
Increased Employee Morale: Quality control measures empower employees to take ownership of their work and contribute to the collective effort of delivering high-quality products. By implementing quality control, businesses foster a culture of excellence and continuous improvement, leading to increased employee morale, job satisfaction, and productivity.
Competitive Advantage: Businesses that prioritize quality control tend to gain a significant competitive edge over their rivals. Consistently delivering high-quality products can differentiate your business from competitors, positioning you as a preferred choice among customers and attracting new opportunities for growth and expansion.
Overall, implementing quality control measures is an essential investment for any business looking to thrive in today’s competitive marketplace. By focusing on quality, businesses can enhance customer satisfaction, increase profitability, improve brand reputation, lower costs, boost employee morale, and gain a competitive advantage. In the long run, these benefits will contribute to the overall success and growth of your business.