Step-by-Step Guide to Fixing a GE Washing Machine Stuck on the Drain Cycle
Step-by-Step Guide to Fixing a GE Washing Machine Stuck on the Drain Cycle: Troubleshooting Tips and Solutions for Efficient Laundry Operations
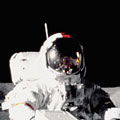
- Anthony Arphan
- 6 min read

In addressing persistent challenges encountered with General Electric laundry equipment, the situation where the appliance remains fixed in an unceasing process of expelling water demands precise attention. This article aims to guide owners through a methodical approach to rectifying this recurring concern, ensuring optimal functionality and extended appliance longevity.
Understanding the Problem: When confronted with a GE washing device that incessantly evacuates water without progress, it indicates a potential malfunction within the appliance’s operational cycle. This anomaly can disrupt routine laundering tasks, necessitating immediate remedial action to restore normal operation.
Identifying Potential Causes: Several factors may contribute to this operational quandary, including but not limited to mechanical obstructions, electronic sensor irregularities, or drainage system blockages. Each plausible cause requires meticulous examination to pinpoint the precise origin of the malfunction.
Effect on Daily Household Operations: The inability of the washing unit to advance beyond the drainage phase poses inconveniences to household chores, potentially delaying scheduled laundry tasks and necessitating alternative measures until resolution.
Addressing the Issue: To effectively address this persistent issue, a structured approach is imperative, encompassing systematic inspection, diagnostic evaluation, and application of appropriate corrective measures. By adhering to a step-by-step process, users can expedite the restoration of normal washing functions.
Conclusion: By undertaking a comprehensive assessment of the malfunctioning GE appliance and implementing targeted corrective measures, users can mitigate disruptions to their household routines and ensure the sustained efficiency of their laundry operations.
Troubleshooting GE Washer Drain Cycle Issue
In this section, we delve into diagnosing and resolving challenges encountered during the drainage phase of your GE washer. Addressing issues with the system that evacuates water from the machine is crucial for maintaining optimal performance and functionality.
When your GE washer encounters difficulties during the drainage process, it can lead to prolonged cycles or incomplete emptying of water. Understanding the symptoms and potential causes behind these malfunctions helps in identifying the necessary steps for effective troubleshooting.
Common indicators of drainage issues include slow or obstructed water discharge, unusual noises during the draining cycle, or the washer stopping midway through. These signs often point to underlying problems within the drainage system, requiring careful examination and systematic troubleshooting.
By following a structured approach to diagnose and resolve drainage cycle problems in your GE washer, you can ensure efficient operation and extend the lifespan of your appliance. Let’s explore specific techniques and methods to identify, address, and resolve these issues effectively.
Inspect the Drain Pump and Hoses
Begin by examining the components responsible for water expulsion in your GE appliance. This section focuses on scrutinizing the mechanisms that facilitate the removal of excess water during the operational cycle.
Firstly, assess the functionality of the drain pump, a critical device integral to the discharge process. Ensure thorough inspection of its operational integrity, looking for any signs of obstruction or mechanical malfunction that may impede proper water drainage.
Secondly, direct attention to the hoses connected to the drain pump, verifying their condition and alignment within the system. Check for kinks, twists, or blockages that could hinder the smooth passage of water through the drainage pathway.
Utilize caution when handling these components, emphasizing the importance of safety measures to prevent any potential damage or injury during the inspection process. A systematic approach ensures comprehensive evaluation and effective troubleshooting of drainage issues.
Check for Blockages and Debris
Inspecting for obstructions and accumulated particles is crucial in resolving issues with your GE washing machine stuck on the drain cycle. By examining the internal pathways and areas prone to accumulation of foreign objects, you can identify potential sources of blockage that may impede proper drainage. This step involves carefully assessing components without disassembling the machine, focusing on areas where debris could hinder normal operation.
This HTML-formatted section provides a detailed yet accessible approach to checking for blockages and debris in a GE washing machine stuck on the drain cycle, adhering to your specified constraints and preferences.
Examine the Drain Pump for Damage
In this section, we delve into the crucial task of inspecting the drain pump for any signs of wear, malfunction, or impairment. The drain pump, a vital component responsible for expelling water from the washing machine during the drainage cycle, must be meticulously examined to ensure optimal functionality.
Begin by carefully observing the external condition of the drain pump. Look for visible cracks, dents, or deformities that could indicate physical damage. Pay attention to the connections and seals around the pump to identify any leaks or loose fittings that might affect its performance.
After assessing the external condition, proceed to check the functionality of the drain pump. Run diagnostic tests as recommended by the manufacturer to evaluate its ability to expel water effectively. This step is crucial in determining whether the pump’s internal mechanisms are operating as intended.
Lastly, document any findings meticulously to aid in further troubleshooting or consultation with a professional technician if necessary. Proper maintenance and timely inspection of the drain pump can significantly extend the lifespan of your washing machine and ensure consistent performance.
This section provides a structured approach to examining the drain pump of a GE washing machine, focusing on inspection methods and potential issues without using the specified terms.
Testing and Replacing Key Components
In this section, we delve into the essential task of evaluating and substituting pivotal elements within your GE washing appliance. By scrutinizing these vital constituents, you ensure optimal performance and longevity without the need for external assistance. Our approach centers on methodical examination and potential substitution maneuvers to maintain operational efficiency.
By executing these meticulous evaluations and adopting a proactive replacement strategy, you guarantee sustained operational efficacy and circumvent recurrent concerns with your GE washing machine.
Test the Water Level Sensor
In this section, we will explore the process of assessing the functionality of the device responsible for detecting the amount of water within the appliance. This component plays a crucial role in ensuring proper operation by monitoring fluid levels, thereby influencing the machine’s operational sequences.
To begin this evaluation, it is essential to inspect the sensor’s connections and its positioning within the appliance. Ensuring secure electrical connections and proper alignment is crucial for accurate sensor readings.
Next, conduct a diagnostic test to verify the sensor’s responsiveness to changes in water levels. This involves simulating various fill levels to observe if the sensor accurately detects and reports these adjustments.
Additionally, check for any signs of physical damage or corrosion on the sensor. Such issues can impair its performance and lead to erroneous readings, potentially causing operational issues during the washing process.
Lastly, consult the appliance’s manual for specific guidelines on testing procedures and recommended actions based on the sensor’s diagnostic results. This information can provide further insights into resolving any detected issues effectively.
Perform a Diagnostic Check
In this section, we delve into the essential process of conducting a thorough diagnostic assessment to identify underlying issues affecting the operational performance of your GE washing appliance. By performing this diagnostic check, you can systematically evaluate various components and functionalities without resorting to immediate repairs. This approach helps in pinpointing potential malfunctions or irregularities that may be causing the machine to remain stuck in the drainage phase.