Essential Steam Cycle Maintenance Tips for Ensuring Longevity
Essential Steam Cycle Maintenance Tips for Ensuring Longevity: Learn how to extend the lifespan and efficiency of your industrial systems with regular inspections, cleaning, and proper care.
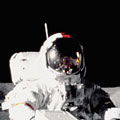
- Anthony Arphan
- 9 min read

Maintaining the efficiency and functionality of your equipment can be challenging, yet it is pivotal for ensuring long-term performance. By implementing a few key practices, you can significantly enhance the durability and operational efficiency of your machinery. These methods not only help in reducing downtime but also save on repair costs, ensuring that your investment remains in optimal condition for years to come.
Regular Check-ups and proactive care are fundamental to preventing unexpected breakdowns. This involves a detailed inspection of various components to identify and address potential issues before they escalate. Additionally, adhering to a consistent upkeep schedule can greatly improve the overall health of your system.
Cleaning and proper handling of your equipment play a crucial role in its longevity. Removing debris and ensuring that all parts are free from obstruction will enhance performance and prevent premature wear. Moreover, using the right cleaning agents and techniques will help in preserving the integrity of the components.
Implementing these strategies is essential to maintaining the smooth operation of your machinery. By prioritizing regular inspections and proper care, you can ensure that your system remains efficient and reliable, ultimately extending its lifespan and maximizing your investment.
Ensuring Longevity: Key Steam Cycle Maintenance Tips
To extend the lifespan and efficiency of your industrial systems, it is crucial to follow a systematic approach to upkeep and care. Consistent and thorough practices can prevent breakdowns and optimize performance, leading to long-term savings and reliability.
Below are some pivotal practices that can help ensure your equipment remains in optimal condition:
Aspect | Recommended Action | Frequency |
---|---|---|
Water Quality | Regularly test and treat water to prevent scaling and corrosion. | Weekly |
Component Inspection | Examine all key parts for signs of wear and tear, and replace as necessary. | Monthly |
Lubrication | Ensure all moving parts are properly lubricated to minimize friction. | Bi-weekly |
System Flush | Perform a full system flush to remove any build-up of residues. | Annually |
Pressure Checks | Monitor and adjust pressure levels to avoid overstressing the system. | Daily |
By adhering to these practices, you can significantly prolong the operational life and efficiency of your equipment, ensuring that it runs smoothly and efficiently for years to come.
Regular Inspection and Cleaning
Regularly inspecting and cleaning your equipment is crucial to ensuring it operates efficiently and has a long service life. By routinely checking for any issues and keeping all components clean, you can prevent small problems from escalating into major repairs. Consistent upkeep not only enhances performance but also contributes to the safety of the system.
Start by establishing a schedule for thorough inspections. Look for signs of wear, corrosion, or any abnormalities that might indicate potential trouble. Paying close attention to these details can help you address problems early, minimizing downtime and repair costs.
Cleaning is equally important. Accumulated dirt, debris, and residues can hinder the functionality of the system. Ensure that all parts are cleaned according to the manufacturer’s guidelines, using appropriate tools and solutions. Regular cleaning helps maintain optimal efficiency and prevents the build-up of contaminants that could impair the operation.
In conclusion, by integrating regular inspections and diligent cleaning into your routine, you can significantly extend the lifespan of your equipment and ensure it runs smoothly and safely. This proactive approach is key to maintaining high performance and avoiding unexpected breakdowns.
Inspecting Components for Wear and Tear
Regular evaluation of machinery is crucial to ensure optimal performance and prevent unexpected breakdowns. By examining each part meticulously, you can identify potential issues early and address them before they escalate into costly repairs.
The inspection process involves several steps, which include observing, measuring, and testing various components. Below are the key aspects to consider during an examination:
Visual Inspection: Look for obvious signs of deterioration, such as cracks, corrosion, or discoloration. Pay special attention to joints and connections where wear is often more pronounced.
Mechanical Testing: Perform tests to evaluate the functionality and integrity of moving parts. This may involve checking the smoothness of bearings, the tension of belts, and the alignment of shafts.
Dimensional Checks: Measure critical dimensions to ensure they remain within specified tolerances. Use calipers, micrometers, or other precision tools to detect any deviations.
Lubrication Assessment: Verify that all lubricated parts are adequately greased and free from contaminants. Check the quality of the lubricants and replace them if necessary.
Thermal Imaging: Utilize thermal cameras to identify hot spots, which can indicate areas of excessive friction or electrical issues. This non-invasive method provides a clear view of temperature variations.
By systematically reviewing each element, you can maintain the reliability and efficiency of your equipment. Early detection of wear and tear not only extends the lifespan of components but also enhances overall operational safety.
Cleaning Internal Surfaces to Prevent Scale Buildup
Maintaining the internal cleanliness of equipment is vital to ensure efficient operation and prolong the life of your machinery. By regularly addressing and removing mineral deposits, you can avoid various issues that can impair functionality and lead to costly repairs. Understanding the importance of this process helps in sustaining optimal performance and minimizing downtime.
One effective strategy to combat mineral accumulation involves using chemical descalers designed to dissolve these deposits. It is important to select the right type of descaler suitable for your specific equipment to ensure thorough cleaning without causing any damage. Follow the manufacturer’s guidelines to achieve the best results.
Another method is mechanical cleaning, which can involve using brushes, scrapers, or other tools to physically remove buildup from the internal surfaces. This approach can be particularly useful for stubborn deposits that are resistant to chemical treatments. Combining both chemical and mechanical methods can often yield the most comprehensive results.
Preventative measures are equally crucial in this context. Implementing water treatment systems, such as softeners or demineralizers, can significantly reduce the likelihood of scale formation. Regular monitoring of water quality and performing routine inspections of internal components will help identify potential issues early and address them before they become severe.
Lastly, documenting each cleaning session and maintaining detailed records will assist in tracking the effectiveness of your efforts and planning future maintenance activities. By adopting these practices, you can ensure that your equipment remains in peak condition, ultimately saving time and resources in the long run.
Optimizing Operating Conditions
Ensuring the efficiency and reliability of your thermal power system is a crucial aspect of extending its operational lifespan. By maintaining optimal conditions during operation, you can significantly enhance performance and reduce the likelihood of unexpected breakdowns. This section delves into various strategies and adjustments that can help achieve ideal operational parameters.
Firstly, monitoring and regulating temperature and pressure levels is paramount. Consistent tracking and adjustment of these variables ensure that the system functions within safe and efficient ranges. Implementing advanced sensors and control systems can aid in achieving this precision.
Additionally, the quality of water used in the system plays a pivotal role. Utilizing high-purity water can prevent the accumulation of impurities and scale, which can otherwise hinder performance and cause damage. Regular testing and treatment of the water supply can mitigate these risks.
Another key factor is the maintenance of mechanical components. Ensuring that all parts are well-lubricated and free from wear and tear will help maintain smooth operations. Regular inspections and timely replacements of worn-out components are essential to avoid mechanical failures.
Finally, integrating a robust monitoring system that provides real-time data and alerts can be a game-changer. This allows for proactive adjustments and quick responses to any anomalies, thereby maintaining optimal conditions and preventing minor issues from escalating into major problems.
Monitoring Steam Pressure and Temperature
In this section, we focus on overseeing the fluctuations in pressure and temperature within the steam system. Understanding these dynamics is crucial for maintaining optimal operational conditions and ensuring the reliability of the equipment. By observing these variables closely, operators can anticipate potential issues before they escalate, thereby enhancing the system’s efficiency and longevity.
- Pressure Observance: Regularly check the pressure gauges to track variations during operation. This allows for timely adjustments to prevent overpressure or underpressure situations, safeguarding components from potential damage.
- Temperature Oversight: Monitor the temperature readings across different points of the steam system. Consistent monitoring helps in identifying deviations that could indicate inefficiencies or operational anomalies.
- Recording and Analysis: Maintain a log of pressure and temperature readings over time. Analyzing historical data aids in identifying trends, allowing for proactive maintenance and optimizing system performance.
- Alert Systems: Implement automated alerts for critical pressure and temperature thresholds. These alerts notify operators of abnormal conditions promptly, enabling swift corrective actions to mitigate risks and maintain system reliability.
By vigilantly monitoring steam pressure and temperature, operators can uphold operational stability, prolong equipment lifespan, and ensure uninterrupted functionality throughout the steam system.
Adjusting Feedwater Quality to Enhance Operational Efficiency
In this section, we explore the optimization of the composition and purity of the water supplied to the boiler system, a critical factor influencing its overall performance. By carefully managing the quality of feedwater, operators can significantly enhance the efficiency and reliability of the steam generation process.
Key Parameters | Optimal Range | Impact |
---|---|---|
Hardness Levels | Low to moderate | Reduces scale formation, minimizing heat transfer inefficiencies |
pH Balance | Neutral to slightly alkaline | Prevents corrosion, prolonging equipment lifespan |
Dissolved Oxygen | Minimal | Reduces oxidative damage to boiler components |
Organic Contaminants | Minimal | Prevents fouling and enhances heat transfer efficiency |
By maintaining these parameters within optimal ranges, operators can ensure that the boiler operates at peak efficiency, minimizing energy consumption and maintenance costs over its operational lifespan.
Implementing Preventive Maintenance Strategies
Incorporating proactive upkeep methods is crucial for sustaining the efficiency and durability of steam system operations over time. By adopting preemptive care approaches, organizations can enhance equipment reliability and minimize unexpected downtime, fostering a more robust operational framework.
Key Strategies | Description |
---|---|
Regular Inspections | Conduct routine assessments to identify potential issues before they escalate, ensuring continuous system functionality. |
Timely Component Replacements | Replace worn-out parts promptly to prevent cascading failures and maintain optimal performance levels. |
Fluid Analysis | Regularly analyze steam quality and fluid composition to mitigate corrosion and improve overall system efficiency. |
Training Programs | Implement training initiatives to educate staff on proper maintenance practices, empowering them to detect and address issues proactively. |
Documentation and Tracking | Maintain comprehensive records of maintenance activities and performance metrics to track trends and facilitate informed decision-making. |
By integrating these preventive strategies into operational protocols, organizations can uphold the integrity and longevity of their steam systems, fostering a culture of reliability and efficiency.
Routine Lubrication of Moving Parts
In the regular care and upkeep of mechanisms that animate, it is imperative to ensure the fluidity and efficiency of motion. This entails the periodic application of lubricants to the various articulations that facilitate movement. By maintaining adequate lubrication, the lifespan of components is prolonged, operational friction is minimized, and the overall performance of the apparatus remains optimized.
Moreover, conscientious attention to lubrication routines mitigates the risk of mechanical malfunction and enhances the reliability of the equipment in operation. Regular inspection and application of suitable lubricants tailored to the specific requirements of each moving part are indispensable practices in the maintenance regimen.